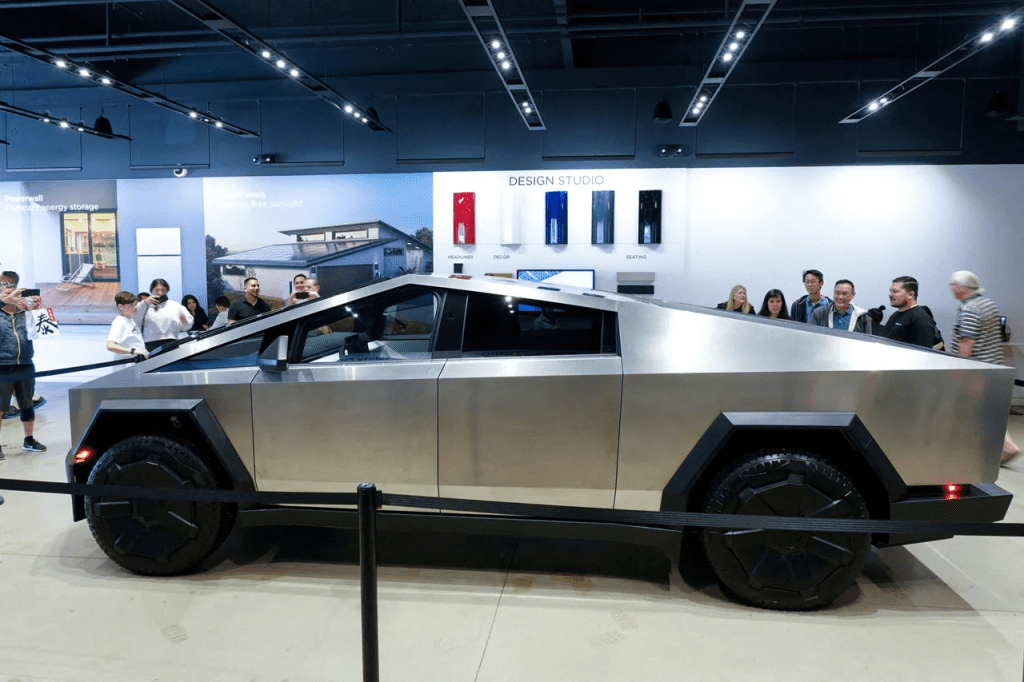
Tesla’s Cybertruck, the angular, stainless steel beast heralded as the future of electric pickups, is facing yet another bump in the road — and this time, it’s literally peeling. A recent recall involving over 46,000 units — nearly every Cybertruck delivered so far — has triggered renewed scrutiny over the vehicle’s quality control. But it’s not just the scale of the recall that has raised eyebrows. It’s the nature of the fix.Glue, patches, and a pair of nuts. That’s the solution. And for some early adopters who shelled out upwards of $100,000, it’s not going down smoothly.
In mid-March 2025, Tesla issued a recall affecting 46,096 Cybertrucks. The defect centers around a steel trim panel — known as the “cant rail” — that runs along the top edge of the side windows. Reports indicate that the panel can become detached while the vehicle is in motion, posing a safety risk not only to the driver but to anyone nearby.
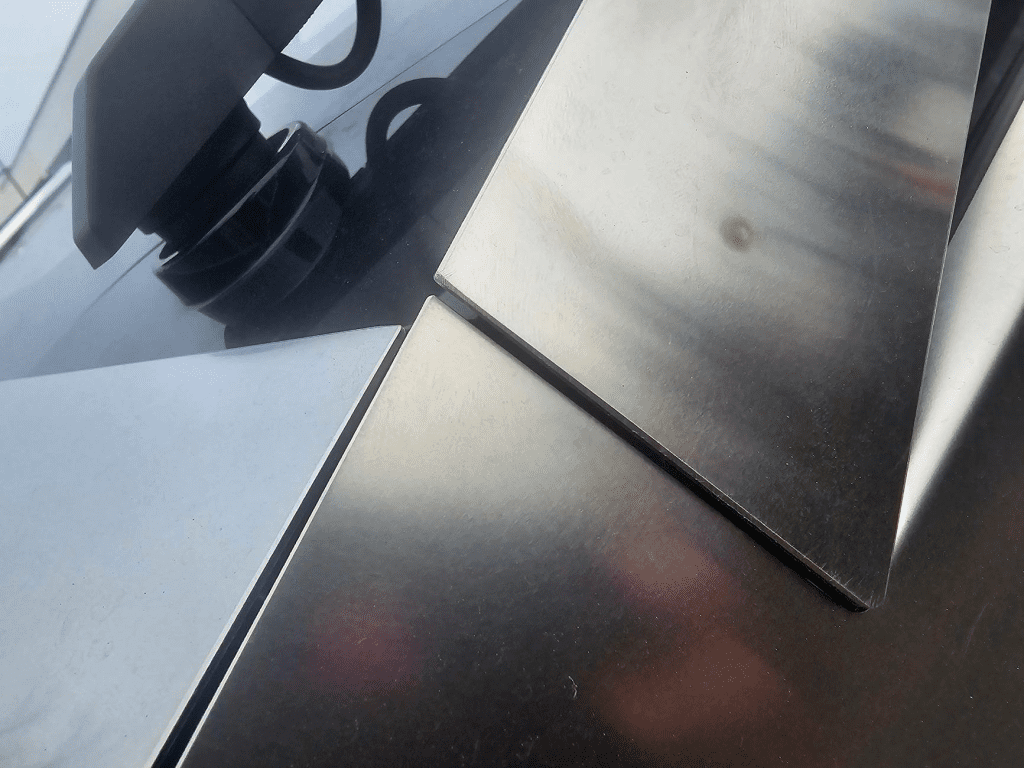
The recall fix, released via Tesla’s internal service bulletin and now publicly known, involves applying butyl adhesive patches to the cant rail, and securing the ends with two new nuts fastened onto existing studs. Depending on the vehicle, techs might apply either two or eight adhesive patches, depending on how secure the panel appears after inspection.The simplicity of the solution might be reassuring in a different context. But for Cybertruck owners who expected military-grade durability and engineering elegance, it feels more like a Band-Aid than a factory-grade repair.While Tesla’s fix may seem straightforward on paper, the real-world execution has already drawn criticism. One Cybertruck owner, posting under the handle @CTDriver on the CybertruckOwnersClub forum, detailed a troubling post-repair experience:“I finally picked up my truck yesterday after the service appointment,” he wrote. “The cantrail trim does NOT look good at all, the gap got tiny bit smaller, but still looks very uneven and misaligned. Plus, a circular burned mark appeared on the base of the new trim piece (welding mark), I also found a patch of scratches on this brand new trim.”
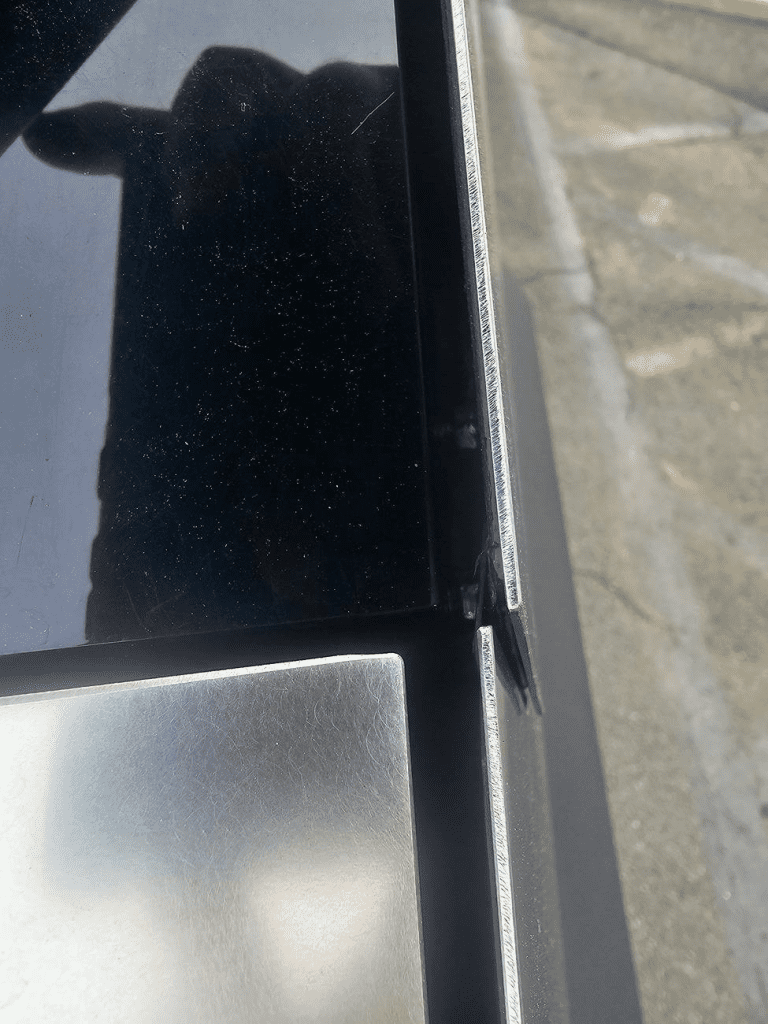
For a vehicle that can cost between $80,000 and $100,000 — and in some cases more due to resale markups or early access premiums — these kinds of cosmetic and quality issues are deeply concerning. What’s worse, the burn mark appears to suggest that some form of heat work — possibly welding or grinding — was performed during the fix, despite Tesla’s official procedure making no mention of it.
“Tesla should NOT do the ‘after-market’ welding at a service center,” the owner continued. “They should produce a clean part from the factory with the bolts/studs already attached. For a major and serious vehicle manufacturer, this is unreasonable and hard to swallow as an early adopter.”Tesla’s repair documentation confirms that many trucks shipped without proper fasteners on the cant rail. The service bulletin outlines how technicians should verify the studs are present and secured with nuts at both ends of the panel. It also provides a video walkthrough of the repair process.The question becomes: how did these trucks leave the factory in the first place without this critical hardware correctly installed?
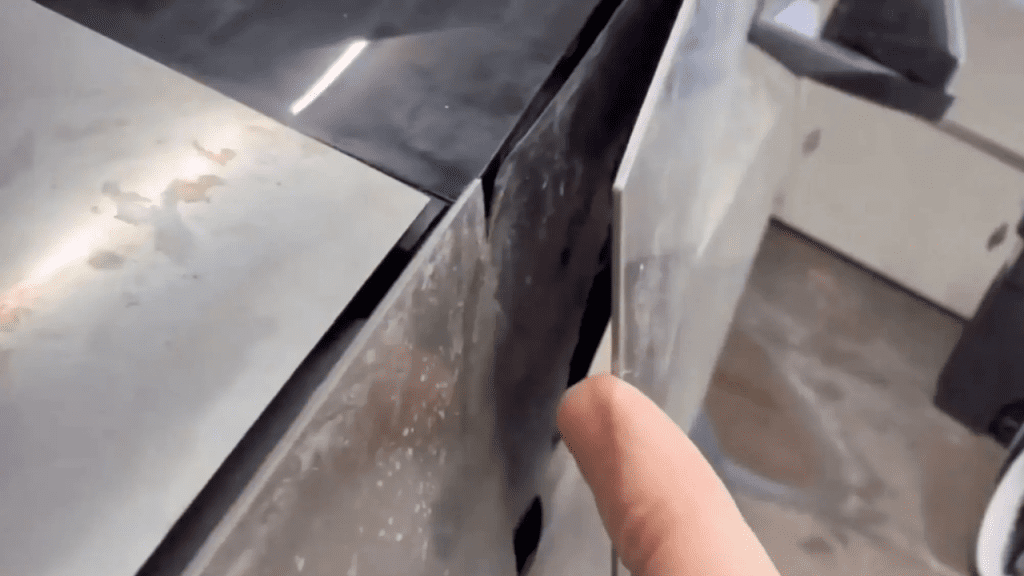
The answer likely lies in Tesla’s history of production iteration — a “build fast, fix later” mentality that has, for better or worse, characterized the company’s approach to manufacturing since the Model S. But while that approach may be tolerable on a $40,000 sedan, it’s a harder sell on a six-figure truck marketed as indestructible.The Cybertruck was supposed to redefine what an electric vehicle could be: rugged, minimalist, futuristic. But with mismatched trim, visible scratches, and makeshift repairs involving glue and nuts, some early adopters are feeling like unpaid beta testers.Another wrinkle in this saga involves Cybertrucks that have been wrapped by third-party shops. Many owners opted to customize their trucks with vinyl wraps in various finishes — matte black, satin white, even camouflage.But Tesla has warned that the recall procedure might damage those wraps when technicians remove and reinstall the cant rail. More troubling still: the company says it won’t reimburse customers for wrap damage, even if it occurs during a mandatory safety recall.
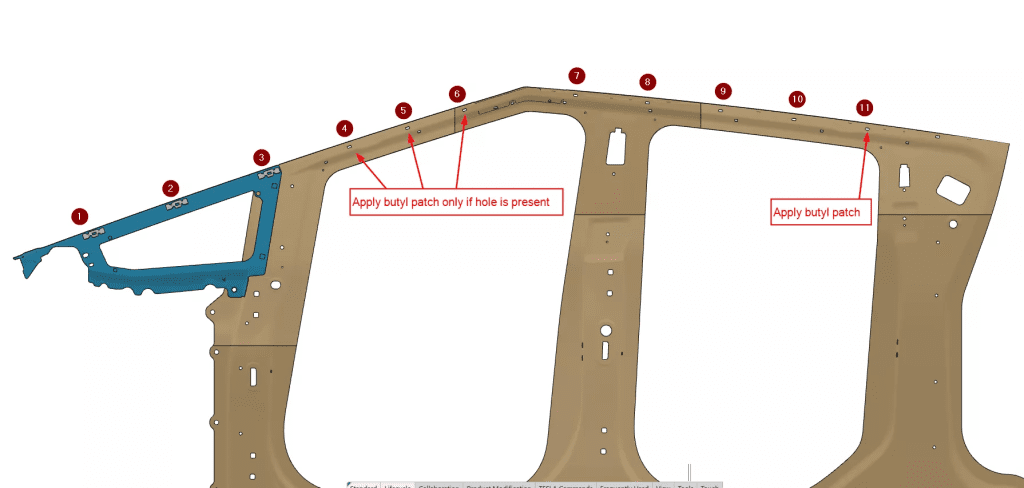
For owners who paid thousands of dollars for their custom wraps, this presents a lose-lose scenario — either risk cosmetic damage, or delay the recall and continue driving a truck with a potentially dangerous flaw.One of the recurring complaints about Tesla’s after-sales service is its inconsistency. With no franchised dealers and a limited number of company-run service centers, Tesla operates under a direct-to-consumer model that prioritizes speed and software-driven diagnostics.But when it comes to physical hardware issues — especially ones involving structural panels — Tesla’s approach can feel under-resourced. Service centers often appear to be stretched thin, with long wait times and questionable quality in execution.That could explain why one owner ended up with scratched panels and heat marks: the technician may not have had the right tools or training, or was rushed through a high-volume recall process.To Tesla’s credit, there’s currently only one documented case of post-repair dissatisfaction circulating in public forums. That doesn’t mean others won’t emerge, but as of now, it’s unclear whether this represents a systemic issue or a one-off misfire.
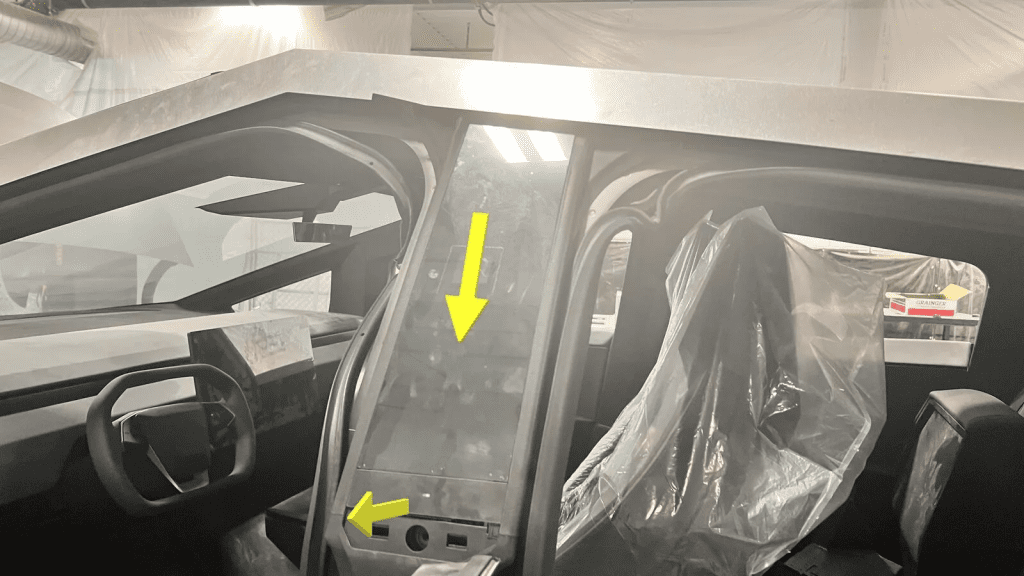
Still, the optics aren’t good. When the solution to a high-profile recall consists of glue, patches, and a pair of nuts, expectations for workmanship climb significantly. Every imperfect repair becomes a potential flashpoint for criticism, especially from a vocal and tech-savvy customer base.And while Tesla’s design team may argue that the fix is structurally sound — and it may well be — the subjective quality experience is another matter entirely.The Cybertruck has always been an exercise in contradiction: brutalist yet high-tech, minimalist yet over-engineered. It’s also Tesla’s most polarizing vehicle to date, with opinions sharply split between die-hard fans and vocal critics.This recall — and the simplicity of its fix — underscores the challenge Tesla faces as it scales production of a highly complex, non-traditional vehicle. The stainless steel exoskeleton, for instance, is harder to work with than traditional automotive sheet metal. That has ripple effects not only in manufacturing but also in repair and maintenance.
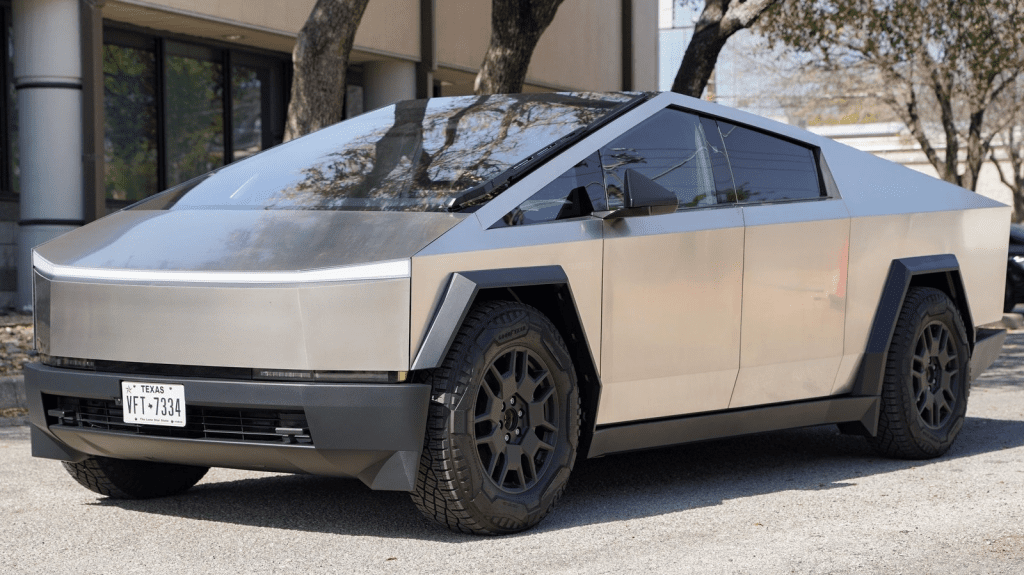
In trying to redefine how vehicles are made, Tesla may have overlooked the mundane realities of trim alignment, part tolerances, and surface finishes. And while that might be forgivable in a prototype or pre-production model, it becomes a liability once trucks are delivered to paying customers.The phrase “Glue, patches, and a pair of nuts” is quickly becoming a meme among Cybertruck owners — a symbol of what happens when cutting-edge design meets corner-cutting repairs. For Tesla, it’s a reminder that innovation and execution must go hand-in-hand.As more Cybertrucks hit the road, we’ll be watching closely to see whether this fix holds up — and whether Tesla can regain the trust of its early adopters, who expected a tank and ended up with a patch job.Until then, one thing is clear: the Cybertruck may be stainless steel, but its reputation isn’t scratch-proof.